When embarking on a construction project in Houston, selecting the right materials and professionals is crucial. Houston concrete solutions offer the durability and versatility needed for both commercial and industrial endeavors. At the forefront of delivering these solutions is Bill Houston Concrete Construction, a company renowned for its commitment to quality and customer satisfaction.
Continue reading “Reliable Concrete Solutions for Houston Projects”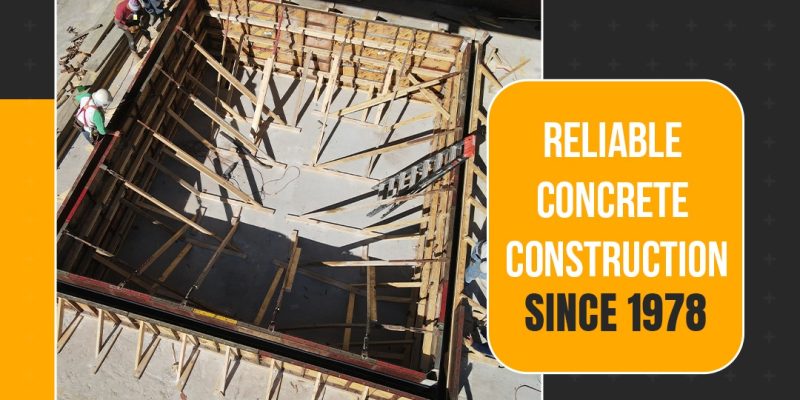